A Basf é a maior empresa química do mundo.
Sua visão para ser mantida até 2.015 inclui,
entre outras metas, formar a melhor equipe da indústria.
Com esta filosofia, o Complexo Industrial de Tintas e
Vernizes, com planta em São Bernardo do Campo,
já saiu na frente, pois foi a primeira planta
da Basf no mundo a utilizar redes de campo. E um dos
dois protocolos definidos foi o Profibus.
Na verdade, o projeto começou em 2000 com a necessidade
da expansão da unidade com a atualização
do SDCD, para o qual se pensava em arquitetura de rede
de barramento.
Segundo Maurício da Silva Lopes, Engenheiro de
Manutenção da Basf, na época a equipe
envolvida com o projeto levantou uma série de
aspectos que seriam decisivos na escolha do protocolo,
destacando-se, entre outros: facilidade de configuração.
redução nos custos; possibilidade de solução
integrada; disponibilidade de ferramentas de diagnóstico;
tendência de evolução da tecnologia;
devices com intercambiabilidade de fornecedores; e quantidade
e porte dos fornecedores disponíveis no mercado.
E o Profibus foi um dos escolhidos, especialmente por
ser um protocolo já difundido na Europa, onde
está a sede da Basf.
Na atualização do sistema (Advant da ABB),
na EP-10 foi implantado o Profibus DP/PA, com três
inversores ligados na rede DP e 105 instrumentos de campo
em Profibus PA, além do Profibus DP com ASi, sendo
13 gateways, cada um com dez válvulas on/off em
média, além de chaves de nível e
sensores indutivos. Já a EP 13 hoje opera também
com Profibus DP/PA, sendo 50 instrumentos de campo em
Profibus PA, e com Profibus DP/ASi, sendo quatro gateways,
cada um igualmente com dez válvulas on/off em
média, e, ainda, chaves de nível e sensores
indutivos.
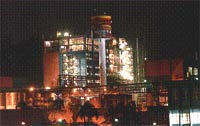
Vista do Complexo Industrial de Tintas e Vernizes: a
estréia em Profibus.
Durante a implementação do protocolo,
naturalmente, surgiram, obstáculos que, na verdade,
foram úteis para o aprendizado: ”Houve falta
de comprometimento dos fornecedores com o funcionamento
da rede, além do que foi preciso montar uma bancada
de teste para configuração da placa da
ABB e teste de comunicação de instrumentos
por tipo e fornecedor. Também percebemos a falta
de conhecimento especifico da maioria dos fornecedores
e, de fato, grande parte deles estava conhecendo a tecnologia
no cliente; não havia especialistas no mercado.
Assim, houve dificuldade de informações
específicas da configuração redes
e instrumentos, tais como: utilização GSD,
mapas de erro, envio e recebimento de telegramas, entre
outros; e, ainda, constávamos que o fornecedor
entregava o equipamento com outro protocolo”, conta
Lopes.
As conseqüências foram, além de um
atraso no cronograma de partida das novas ruas do reator
e, a necessidade da consulta a um especialista europeu
no protocolo do fornecedor e a sua colaboração
para ajudar no funcionamento dos equipamentos de outros
fornecedores. “Tivemos também problemas
com o tempo de varredura da placa de comunicação
do SDCD, devido à grande quantidade de instrumentos
na rede”, completa o Engenheiro de Manutenção.
Contudo, a empresa se preparou – e bem – para
a implementação. Promoveu o treinamento
dos profissionais da manutenção nos equipamentos
e tecnologias executados pelo grupo da Basf, o que foi
reforçado com palestras técnicas ministradas
pelo fornecedor e a disponibilização de
literatura técnica sobre as tecnologias e os produtos.
O retorno com a implementação do Profibus
foi positivo e, no primeiro semestre de 2002, a Basf
iniciou um segundo projeto, agora na automação
dos sistemas de tancagem, especialmente no descarregamento
e carregamento de caminhões, por meio do monitoramento
e intertravamento de níveis. O recebimento ou
envio de sinais é composto de: 88 radares (através
de gateways Profibus DP/PA); válvulas (através
de gateways Profibus DP/ASi); bombas (módulos
de entrada e saída digitais); 88 chaves de nível
(módulos de entrada digital); IHM (através
de gateway Profibus DP/RS 422); entre CLPs (através
de rede Profibus DP); e entre SDCD e CLPs (através
de gateways DP/DP). A configuração da rede é composta
por: 102 sinais AI – Couplers Profibus DP/PA (indicação
nível/ temperatura); 920 sinais DI –Gateways
Profibus DP/AS-i (válvulas on/off e manuais);
48 sinais DO – Gateways Profibus DP/AS-i (válvulas
pilotadas); 90 Sinais DO – Módulos de saída
digitais (acionamento de bombas); e 80 sinais DI – Módulos
de entrada digital (chaves de nível).
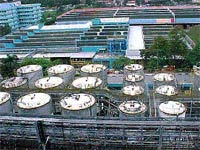
Sistema de tancagem da Basf, contemplado no segundo projeto
com Profibus.
O terceiro projeto em Profibus começou no segundo
semestre de 2003 na nova fábrica da Suvinil, com
vistas ao à supervisão das etapas de produção,
especialmente na dispersão (empastamento) e na
fabricação (texturado e completação).
A configuração da rede inclui: centralização
de sinais em um único CLP; analógicos através
de gateways Profibus DP/PA e módulos analógicos;
válvulas através de gateways Profibus DP/ASi;
bombas com módulos de entrada e saída digitais;
inversores diretamente na rede DP; IHM com operação
em Profibus DP e confirmação em MPI; 24
sinais AI – Couplers Profibus DP/PA (indicação
de vazão e nível); 500 sinais DI – Gateways
Profibus DP/ASi (válvulas on/off e manuais); 230
sinais DO – Gateways Profibus DP/ASi (válvulas
on/off e manuais); 190 sinais DO – Módulos
de saída digitais (válvulas e bombas);
e 380 sinais DI –Módulos de entrada digital
(nível, válvulas, bombas, botoeiras).
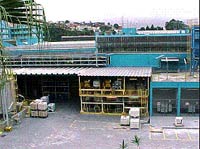
Nova fábrica da Suvinil: o terceiro projeto em
Profibus.
O mais recente projeto da Basf com Profibus foi concluído
há pouco mais de dois meses para a automação
de aquecedores e caldeiras. A rede está configurada
da seguinte forma: centralização de sinais
em um único CLP; sinais analógicos e digitais
entre CLPs através de rede DH485; e entre SDCD
e CLPs por meio de placa de comunicação
Profibus DP para CLPs Allen-Bradley; 30 sinais AI –Gateway
Profibus DP/DP (indicação de vazão,
pressão e temperatura); 250 sinais DI – Placa
Profibus DP (válvulas on/off e manuais); e 48
sinais DO – Placa Profibus DP (válvulas
pilotadas, partida e parada, bombas).
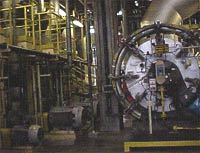
Caldeiras: projeto mais recente da Basf com Profibus.
Depois do quatro projetos Lopes afirma que, além
do grande aprendizado para a equipe, a percepção
vem dos fornecedores: “Alguns desenvolvem mais
o seu pessoal, especialmente os de assistência
técnica, do que outros. É um detalhe a
ser destacado.”, conclui.