EVOLUÇÃO DA MEDIÇÃO DA TEMPERATURA E DETALHES DE UM TRANSMISSOR DE TEMPERATURA PROFIBUS-PA
Marco A. Graton, Engenheiro de Desenvolvimento Eletrônico, e César Cassiolato, Gerente de Produtos, da Smar Equipamentos Industriais Ltda.
Introdução
É notável o avanço da Física e eletrônica nos últimos anos. Sem dúvida de todas as áreas técnicas, foram as mais marcantes em desenvolvimentos.Hoje somos incapazes de viver sem as facilidades e benefícios que estas áreas nos proporcionam em nossas rotinas diárias. Nos processos e controles industriais não é diferente, somos testemunhas dos avanços tecnológicos com o advento dos microprocessadores e componentes eletrônicos, da tecnologia Fieldbus, o uso da Internet, etc.
Um pouco de história
O corpo humano é um péssimo termômetro, pois só consegue diferenciar o que esta frio ou quente em relação à sua própria temperatura. Portanto com o passar dos tempos o homem começou a criar aparelhos que o auxiliassem nesta tarefa. Vejamos a seguir mais detalhes.
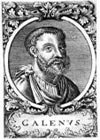
|
Uma das primeiras tentativas de construção de uma escala de temperatura ocorreu por volta de 170 DC . Claudius Galenus of Pergamum (130-201), medico grego, teria sugerido que as sensações de “quente” e “frio” fossem medidas com base em uma escala com quatro divisões numeradas acima e abaixo de um ponto neutro. Para tal escala termométrica, atribuiu a temperatura de “quatro graus de calor” à água a fervendo, a temperatura de “quatro graus de frio” ao gelo e a temperatura “neutra” a uma mistura de quantidades iguais daquelas duas substâncias. Galen não foi um excelente medico, mas sim um excelente fisiologista. Ele escreveu vários tratados médicos, frutos de seu trabalho no tratamento dos Gladiadores romanos e das suas dissecações de animais vivos. Ele foi o primeiro medico a dar diagnósticos pela medição do pulso da pessoa. |
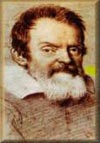
|
O primeiro termômetro foi idealizado por Galileu Galilei (1564-1642). Ele consistia de um longo tubo de vidro com um bulbo preenchido com vinho. Este primeiro tipo de aparelho utilizado para a medição de temperatura foi chamado de termoscópio (instrumento que indica a temperatura através da mudança do volume). Alguns tinham o ar do bulbo retirado antes de se colocar o liquido (podia ser água colorida no lugar do vinho), fazendo com que o liquido subisse dentro do tubo. Conforme o ar restante no tubo era aquecido ou esfriado, o liquido do tubo variava refletindo a mudança na temperatura do ar. Mais tarde seu colega Sanctorius Sanctorius acrescentou uma escala gravada no tubo para facilitar a medição da alteração da temperatura. |
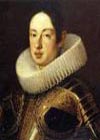
|
Como o vinho era altamente influenciado pela pressão atmosférica, em 1641 Fernando II, Grão-Duque da Toscana (1610-1670) desenvolveu o primeiro termômetro selado. Ele utilizou o álcool em seu interior e fez 50 marcas (graus) na sua haste. Este termômetro não utilizava nenhum ponto fixo para a calibração da escala. O termômetro com utilização de substancia orgânica (álcool, etc) em seu interior passou a ser conhecido como termômetro “spirit”. |
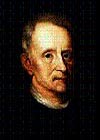
|
Robert Hook (1635-1703) , curador da Sociedade Real em 1664 usou tintura vermelha no álcool. Sua escala, na qual cada grau representava um incremento do volume equivalente a 1/500 parte do volume do liquido do termômetro precisava somente de um ponto fixo. Ele selecionou o ponto de congelamento da água.
O termômetro original de Hook tornou-se padrão do Colégio Gresham e foi usado pela Sociedade Real até 1709. A primeira leitura meteorológica compreensível foi feita nesta escala. |
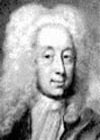
|
Em 1701, Ole Christensen Rømer (1644-1710) criou o primeiro termômetro, com dois pontos de referencia. O termômetro usava vinho vermelho como indicador da temperatura. Rømer criou a escala de seu termômetro com 60 representando o ponto de ebulição da água. Rømer não sabia que o ponto de ebulição da água dependia da pressão atmosférica, fato descoberto depois por Fahrenheit. Quanto ao ponto inferior, isto é questão de debate já que partes de suas anotações foram destruídas pelo fogo. Alguns dizem que 0 representava uma mistura de água, gelo e cloreto de amônia, outros que ele usou o ponto de desgelo da água que marcou com 7.2 Rø. Mais tarde Rømer adotou por razões praticas outros pontos de referencia como a água congelada e a temperatura do sangue (temperatura do corpo humano) que ele marcou como 22.5 Rø. Apesar da criação do termômetro, Rømer é mais conhecido pelo seu trabalho com a medição da velocidade da luz. |
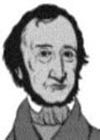
|
Daniel Gabriel Fahrenheit (1686-1736) devotou a maior parte de sua vida a criação de instrumentos meteorológicos. Em 1708, Fahrenheit visitou Rømer em Copenhague e viu seu termômetro com dois pontos de calibração. Impressionado com o termômetro, ele passou a utilizá-lo quando voltou à Alemanha. Mais tarde, não gostando do inconveniente (e das frações) de dividir os graus Rømer de modo a permitir a medição de pequenos intervalos de temperatura e ele multiplicou a escala de Rømer por 4. Isto fez com que o ponto de derretimento da água fosse 30 graus e a temperatura do copo humano 90 graus. Depois ele mudou estes valores para 32 e 96 graus respectivamente para simplificar a marcação da escala (em 64 divisões).
Fahrenheit ainda adicionou mais um ponto com referencia, a temperatura de equilíbrio de uma mistura de gelo e sal, que foi definida como zero em sua escala. Infelizmente o uso de três referencias causou mais incerteza do que precisão. Após a morte de Fahrenheit, a temperatura do corpo humano foi considerada inconstante para a definição de um ponto na escala de temperatura, então sua escala foi modificada para dar a ela novamente 2 pontos de referencia. Tudo isto resultou no desajeitado padrão numérico, com o ponto de congelamento da água definido como 32 F e o ponto de ebulição (na pressão atmosférica padrão) definido como 212 F. Fahrenheit também percebeu que o álcool não tinha precisão e repetibilidade para a medição da temperatura. Em 1714, ele adotou o mercúrio, o qual se mostrou uma excelente alternativa devido ao seu coeficiente de expansão térmica ser altamente linear e não se dissolver no ar. Por outro lado ele é menos sensível a mudança de temperatura. |
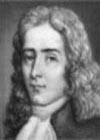
|
Em 1731, Réne Antoine Ferchault de Réamur (1683-1757) propôs uma escala diferente, calibrada em apenas um ponto com as divisões da escala baseada na expansão do fluido no termômetro. Réamur fez muitos experimentos para selecionar o fluido termometricamente adequado e estabeleceu o conhaque diluído em uma certa quantidade de água. A diluição escolhida foi uma que dava a diluição de 80 em 1000, conforme aquecido da temperatura do congelamento até a temperatura de ebulição da água (80 porque era um numero fácil de se dividir em partes). Por causa desta seleção, as pessoas passaram a acreditar que na escala de Réamur a água fervia em 80 graus. Devido a isto, a escala de Réamur passou a ser graduada utilizando dois pontos fixos, o ponto de congelamento (0) e o ponto de ebulição da água (80). Esta escala foi oficialmente adotada na Europa, exceto na Grã-bretanha e na Escandinávia, mas com a adoção da escala centígrados pelo governo revolucionário da França em 1794 ela gradualmente perdeu popularidade e finalmente caiu em desuso no século 20. |
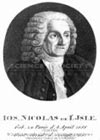
|
Um termômetro com escala similar a de Réamur foi inventada em 1732 por Joseph Nicolas Delisle (1688-1768), astrônomo francês, que foi convidado para ir a Rússia por Pedro, o grande. Naquele ano ele construiu um termômetro que usava mercúrio com fluido de trabalho. Delisle escolheu sua escala usando a temperatura de ebulição da água como o ponto fixo e mediu a contração do mercúrio (com baixas temperaturas) em cem milésimos. Os termômetros antigamente tinham 2400 graduações apropriadas ao inverno em São Petersburgo onde Delisle viveu. Em 1738 Josias Weitbrecht (1702 - 1747) recalibrou o termômetro de Delisle com 0 grau como o ponto de ebulição da água e 150 graus como o ponto de congelamento da água. Este termômetro permaneceu em uso na Rússia por mais de um século. |
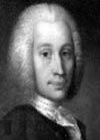
|
Muitas tentativas de transformar a escala de Delisle para um intervalo de 100 graus foram feitas antes que o Suíço Anders Celsius (1701-1744) em 1742 propusesse graduar o termômetro com 100 graus como o ponto de ebulição da água e 0 como o ponto de derretimento da neve.
Aparentemente desejando evitar o uso de números negativos para as temperaturas, Celsius determinou o numero 100 para o ponto de congelamento da água e 0 para o ponto de ebulição, dividindo a distancia em intervalos de 100 graus. |
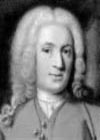
|
Em 1744 o amigo de Celsius, Carl Linnaeus (1707-1778) inverteu a escala centígrado para atender um sentimento psicológico que quente deveria corresponder a maior temperatura. O uso da escala de Celsius no século 19 foi acelerado pela decisão das autoridades revolucionarias da França de adotar o sistema decimal para todas a quantidades mensuráveis. A escala centígrado tornou-se popular primeiro na Suíça e na Franca (onde ela coexistiu com a escalar de Réaumur) e depois na maior parte do mundo. A comissão de Pesos e Medidas, criado pela Assembléia Francesa decidiu em 1794 que o grau termométrico seria 1/100 da distancia entre o ponto do gelo e o vapor d'água (originando a palavra centígrado). Em outubro de 1948 na IX conferencia de Pesos e Medidas o nome da unidade foi alterado para Celsius. |
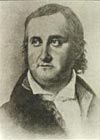
|
Em 1821 Thomas Seebeck (1770-1831), descobriu que quando dois fios de metais diferentes são unidos em duas extremidades e um dos extremos é aquecido circula uma corrente elétrica no circuito. Estava desta forma descoberto o termopar, hoje em dia o mais importante sensor de temperatura para aplicações industriais.
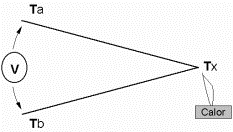
|

|
Sir Humphrey Davy (1778-1829) foi um brilhante cientista responsável pelo uso do gás do riso (oxido nitroso) como anestésico e por algumas descobertas como: o elemento sódio, potássio, boro, a solda por arco elétrico e a lâmpada de segurança para a mineração. Em 1821, ele descobriu também que a resistividade dos metais apresentava uma forte dependência da temperatura. |
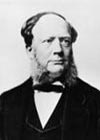
|
Baseado na idéia da resistividade dos metais, Sir William Siemens ( 1823–1883) propôs em 1861, o uso de termômetros de resistência de platina, com o qual a medição da temperatura seria feita à custa da variação da resistência elétrica de um fio de platina com a temperatura. A escolha da platina se deu por ela não se oxidar em altas temperaturas e por ter uma variação uniforme da resistência com a temperatura em um amplo range. |
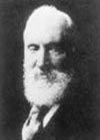
|
Em 1848, William Thomson (1824-1907) desenvolveu uma escala termodinâmica baseada no coeficiente de expansão de um gás ideal.
Está idéia se deve a descoberta de Jacques Charles sobre a variação de volumes dos gases em função da variação da temperatura, onde Charles concluíra com bases em experimentos e cálculos que à temperatura de –273 ºC todos os gases teriam o volume igual a zero. Kelvin propôs outra solução: não era o volume da matéria que se anularia nessa temperatura, mas sim a energia cinética de suas moléculas. Sugeriu então que essa temperatura deveria ser considerada a mais baixa possível e chamou-a se zero absoluto. Então foi criada uma nova escala baseada na escala de grau centígrado. Esta escala absoluta foi mais tarde renomeada para Kelvin e sua unidade designada graus Kelvin (símbolo °K). Observe que a unidade de temperatura no SI é chamada de Kelvin (não graus Kelvin). |
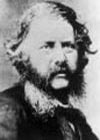
|
Em 1859, William John Macquorn Rankine (1820-1872) propôs outra escala de temperatura na qual especificava 0 para o zero absoluto, mas usava como base a escala graus Fahrenheit. Devido à escala de Rankine ter o mesmo tamanho da escala de Fahrenheit, o ponto de congelamento da água (32ºF) e o ponto de ebulição da água (212ºF) correspondem respectivamente a 491.67°Ra e 671.67°Ra. Esta escala foi mais tarde renomeada Rankine e sua unidade designada graus Rankine (símbolo °R). |
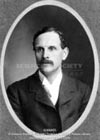
|
Em 1887, Hugh Longbourne Callendar (1863-1930), aperfeiçoou o termômetro com resistência de platina, obtendo grande concordância de resultados entre o termômetro de platina e um termômetro de gás. Atualmente a medição de temperaturas por meio de termômetros de platina assume grande importância em numerosos processos de controle industrial |
A temperatura e os dias de hoje
Com a criação das diversas escalas, houve a necessidade da definição das curvas dos vários sensores e de seus pontos de calibração. Isto foi alcançado nas diversas reuniões desde 1889 até hoje, onde finalmente chegamos ao ITS-90 (International Temperature Scale), mas esta é uma longa historia.
Atualmente as escalas mais utilizadas são Celsius e Fahrenheit. Kevin e Rankine são mais utilizadas por cientistas e engenheiros. Quanto às outras escalas, elas acabaram sendo esquecidas.
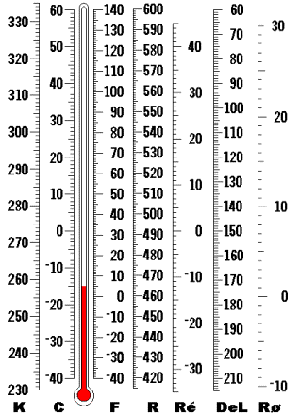
Figura 1 – Comparação das escalas de temperatura.
Várias normas e padrões dependendo do país e região são utilizadas na medição de temperatura: ANSI (EUA), DIN (Alemanha), JIS (Japão), BS (Inglaterra), etc.
Nesta evolução da medição de temperatura, os Transmissores de Temperatura são muito importantes na área de automação e controle de processos. Em conjunto com uma diversidade de sensores contribuem para a melhoria contínua dos processos e qualidade final dos produtos. Veremos a seguir mais alguns detalhes deste importante equipamento.
O mercado e os transmissores de temperatura inteligentes
Analisando o mercado, podemos observar 3 linhas de transmissores de temperatura associados com a aplicação e custo. Um transmissor inteligente combina a tecnologia do sensor mais sua eletrônica.
- Transmissores à prova de explosão e à prova de tempo
Normalmente utilizados em aplicações críticas, com alta e média performance, possuem carcaça com duplo compartimento, separando eletrônica e sensores, dando robustez, segurança e confiabilidade, possuem indicação local, autodiagnose, comunicação digital, ajuste local e são utilizados com os mais diversos sensores em medições simples, dupla, diferencial, sensor backup, etc. Exemplo: TT301(HART/4-20mA), TT302(FF) e TT303(Profibus-PA) da Smar.
- Transmissores para painel, montagem em trilho DIN
São a primeira escolha quando o foco principal é monitoração, permitindo fácil instalação, inúmeras opções em ambientes fechados e conexões com sensores, alta flexibilidade de instalação e manutenção, dando segurança e confiabilidade, possuem autodiagnose, sensor matching (Callendar Van Dusen), comunicação digital e são utilizados com os mais diversos sensores em medições simples, dupla, máxima, mínima, média, diferencial, etc. Exemplo: TT411(HART/4-20mA) da Smar.
- Transmissores para montagem em cabeçote (poço)
São a primeira escolha quando o foco principal é a montagem em cabeçotes, permitindo fácil instalação e conexões com sensores, alta flexibilidade de instalação e manutenção, dando segurança e confiabilidade, possuem auto-diagnose, sensor matching (Callendar Van Dusen),
comunicação digital e são utilizados com os mais diversos sensores em medições simples, dupla, máxima, mínima, média, diferencial, etc. Exemplo: TT421(HART/4-20mA) da Smar.
Em termos de protocolos, como com qualquer outro equipamento de campo, o predomínio no mercado é por protocolos abertos. Vamos ver agora detalhes do TT303, Transmissor de Temperatura Profibus PA.
A figura 2 mostra o diagrama hardware deste transmissor:
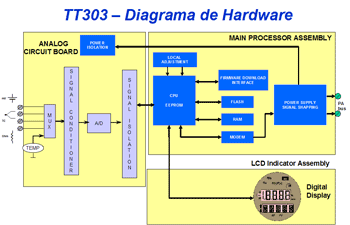
Figura 2 – TT303 – Diagrama De Hardware.
A figura 3 mostra o diagrama funcional deste transmissor:
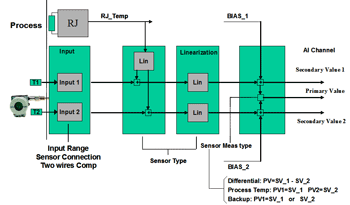
Figura 3- TT303 – Diagrama Funcional.
Este transmissor possui as seguintes características:
- Entrada Universal com ampla escolha de sensores: RTDs padrões, Termopares padrões, ohm, mV e Sensor Especial
- Medição Simples, dupla ou Diferencial: 2 , 3 ou 4 fios e sensor backup
- Isolado
- Compensação de junta fria
- Compensação de resistência de linha
- 0.02% de precisão básica
- Protocolo Profibus-PA
- Re-range
- Autodiagnósticos
- Fácil upgrade para Foundation Fieldbus
- Display (permite 4 posições de montagem)
- Montagem em campo
- À prova de explosão e tempo
- Intrinsecamente Seguro
- Alta Imunidade a EMI e RF
- Robusto
- Ajuste local
- Proteção de escrita
- Verdadeira carcaça com duplo compartimento
Benefícios:
- Baixo custo com manutenção
- Autodiagnóstico remoto
- Somente um modelo de sobressalente para estoque: um único transmissor para qualquer aplicação e ampla faixa e tipo de sensores
- Baixo custo de instalação
- Configuração remota ou local e fácil calibração (re-range)
- Flexibilidade, um único transmissor para qualquer aplicação e ampla faixa e tipo de sensores
- Redução dos custos de produção
- Redução do tempo de paradas (process downtime)
- Melhor uniformidade da produção
- Redução da variabilidade dos processos: economia de matéria-prima e melhor qualidade final do produto devido à alta exatidão e estabilidade.
PROFILE V3.0
Um sistema PROFIBUS pode ser operado e monitorado independentemente de equipamentos e fabricantes se todas as funcionalidades e parametrização, bem como as maneiras de acessos a estas informações forem padrões. Estes padrões são determinados pelos profiles (perfis) do PROFIBUS-PA.
Estes profiles especificam como os fabricantes devem implementar os objetos de comunicação, variáveis e parâmetros, segundo a classe de funcionamentos dos equipamentos. E ainda existe a classificação dos próprios parâmetros:
- Valores dinâmicos de processo: que dizem respeito as variáveis de processo, cuja informação é descrita nos arquivos GSD (device data master) e que serão lidas ciclicamente pelos mestres classe 1 e também aciclicamente pelos mestres classe 2.
Mestre Classe 1: Classe 1 - responsável pelas operações cíclicas (leituras/escritas)
e controle das malhas abertas e fechadas do sistema.
Mestre Classe 2: Classe 2 - responsável pelos acessos acíclicos dos parâmetros
e funções dos equipamentos PA (estação de engenharia : exemplo Profibus View – Smar, PDM-Siemens, Ferramentas baseadas em EDDL, FDT/DTM, etc).
- Valores padrões de configuração/operação: que são exclusivamente acessadas para leitura e escrita vias serviços acíclicas. Existem parâmetros que são mandatoriamente implementados e outros que são opcionais aos fabricantes.
- Parâmetros específicos dos fabricantes: que são exclusivos segundo a funcionalidade daquele fabricante de equipamento e que podem ser acessados aciclicamente, uma vez que também são definidos segundo os padrões de estruturas de dados do profile.
Atualmente, o PROFIBUS-PA está definido segundo o PROFILE 3.0 (desde 1999), onde se tem informações para vários tipos de equipamentos, como transmissores de pressão, de temperatura, posicionadores de válvula, etc.
Estes equipamentos são implementados segundo o modelo de blocos funcionais (Function Blocks), onde se tem o agrupamento de parâmetros que garante um acesso uniforme e sistemático das informações.
Vários blocos e funções são necessários, dependendo do modo e fase de operação. Basicamente, poderiam ser citados os seguintes blocos:
- Blocos Funcionais de entrada e saída analógicas: estes blocos descrevem funcionalidades durante a operação, tais como, troca de dados cíclicos de entrada/saída, condições de alarmes, limites, etc.
- Bloco Físico (Physical Block): que trás informações de identificação do equipamento, assim como, pertinentes ao hardware e software.
- Blocos Transdutores (Transducer Blocks): que fazem o acondicionamento de informações dos sensores que serão utilizadas pelos blocos funcionais e que também recebem informações destes para dispararem atuações em elementos finais de controle.Normalmente um equipamento de entrada (um transmissor de pressão, por exemplo) possui um bloco transdutor (TRD) que está amarrado via canal a um bloco de entrada analógica (AI) e um equipamento de saída (um posicionador de válvula, por exemplo) possui um bloco de saída analógica (AO) que recebe um valor de setpoint e o disponibiliza via canal a um bloco transdutor (TRD) que acionará o elemento final (por exemplo, posicionando uma válvula).
Existem alguns equipamentos que possuem vários blocos AI´s e AO´s e são chamados de equipamentos multicanais, onde se deve ter vários blocos TRD´s associados ao hardware.
O PROFIBUS-PA ainda diferencia os profiles em classes:
- Equipamento Classe A: inclui informações somente dos blocos físico e de funções.Neste tipo de classe, o equipamento está limitado ao básico necessário para operação:variável do processo (valor e status), unidade e tag.
- Equipamento Classe B: possuem funções estendidas de informações dos blocos físico, transdutor e de funções.
Uma característica poderosa suportada pelo PROFILE 3.0 é a definição de cada equipamento segundo os arquivos GSD.Este arquivos garante que qualquer sistema Profibus possa integrar o equipamento, independente de suas características.Com isto cada fabricante pode desenvolver suas particularidades em formas de blocos funcionais que vão além do que está definido no profile.Isto agrega valores nos equipamentos e torna possível a competição de desenvolvimento e oferta de características adicionais nos equipamentos pelos fabricantes.Sendo que as particularidades específicas de cada equipamento podem ser acessadas via conceitos padrões de interfaces, baseado em EDDL (Linguagem Eletrônica Descritiva de Equipamentos) ou FDT (Ferramenta de Equipamento de Campo).Através destas interfaces, o usuário ganha versatilidade e flexibilidade de configuração, parametrização, calibração e principalmente mecanismos de download e upload durante a fase de planejamento/comissionamento dos projetos. A Smar disponibiliza gratuitamente em www.smar.com.br os arquivos EDDL e DTM.
O TT303 possui os seguintes blocos funcionais:
- Bloco Físico (PHY BLOCK): este bloco também é conhecido por bloco de informação do equipamento, onde se tem revisão de software, revisões de hardware, revisões de DD, etc.
- Bloco Transdutor (TRD BLOCK): possui 2 blocos deste tipo, um para canal de temperatura.Este bloco é responsável pelo interfaceamento do sensor com o blocos de entrada analógica (AI). Além disso, trás informações de faixa, data, local e método de calibração, diagnósticos, etc…
- Bloco de Entrada Analógica (AI BLOCK): possui 2 blocos, um para canal de temperatura.
- Bloco Display (DSP BLOCK): é um bloco especial da Smar que permite a configuração dos parâmetros que poderão ser monitorados ou configurados via ajuste local (LCD).
Destes blocos, os blocos AIs farão parte dos serviços de troca de dados cíclicos com o mestre que serão detalhados posteriormente no arquivo GSD.
Mecanismos de comunicação
Tanto o PROFIBUS-DP quanto o PROFIBUS-PA prevêem mecanismos no protocolo contra falhas e erros de comunicação e, por exemplo, durante a inicialização, várias fontes de erros são verificadas. Apos a energização (conhecida como power up) os equipamentos de campo (os escravos) estão prontos para a troca de dados cíclicos com o mestre classe 1, mas para isto, a parametrização no mestre para aquele escravo deve estar correta. Estas informações são obtidas através dos arquivos GSD, que deve ser um para cada equipamento. Veja a seguir, o gsd para o TT303 na figura 4.
Através dos comandos abaixo, o mestre executa todo processo de inicialização com equipamentos PROFIBUS-PA:
- Get_Cfg: carrega a configuração dos escravos e verifica a configuração da rede;
- Set_Prm: escreve em parâmetros dos escravos e executa serviços de parametrização da rede;
- Set_Cfg: configura os escravos segundo entradas e saídas;
- Get_Cfg: um segundo comando, onde o mestre verificará a configuração dos escravos.
Todos estes serviços são baseados nas informações obtidas dos arquivos gsd dos escravos.
Observando o exemplo da figura 4, vê-se que o GSD trás detalhes de revisão de hardware e software, bus timing do equipamento e informações sobre a troca de dados cíclicos. O TT303 possui 2 blocos funcionais: 2 AIs. Além disso, possui o módulo vazio (Empty módulo) para aplicações onde se quer configurar apenas um blocos funcional, de acordo com o tipo de medição de temperatura..
Deve-se respeitar a seguinte ordem cíclica dos blocos: AI_1, AI_2.Vamos admitir que se queira trabalhar somente com um blocos AI, sendo assim, deve-se configurar: AI_1, EMPTY_MODULE.
#Profibus_DP GSD_Revision = 2 Vendor_Name = "SMAR" Model_Name = "TT303" Revision = "1.0" Ident_Number = 0x089a; 2AI Protocol_Ident = 0 Station_Type = 0 Bitmap_Device = "Src089an" FMS_supp = 0 Hardware_Release = "3.0" Software_Release = "1.29" 31.25_supp = 1 45.45_supp = 1 93.75_supp = 1 187.5_supp = 1 MaxTsdr_31.25 = 100 MaxTsdr_45.45 = 250 MaxTsdr_93.75 = 1000 MaxTsdr_187.5 = 1000 Redundancy = 0 Repeater_Ctrl_Sig = 0 24V_Pins = 0 Freeze_Mode_supp = 0 Sync_Mode_supp = 0 Auto_Baud_supp = 0 Set_Slave_Add_supp = 1 Min_Slave_Intervall = 250 Modular_Station = 1 Max_Module = 6 Max_Input_Len = 30 Max_Output_Len = 6 Max_Data_Len = 36 Max_Diag_Data_Len = 14 Slave_Family = 12 User_Prm_Data_Len = 0
|
;Modules for Analog Input Module = "Analog Input ( short )" 0x94 EndModule Module = "Analog Input ( long )" 0x42, 0x84, 0x08, 0x05 EndModule .Empty module Module = "EMPTY_MODULE" 0x00 EndModule |
Figura 4 – Arquivo GSD do TT303.
A maioria dos configuradores PROFIBUS utiliza-se de dois diretórios onde se deve ter os arquivos gsd’s e bitmap’s dos diversos fabricantes. Os gsd’s e bitmap’s para os equipamentos da Smar podem ser adquiridos via internet no site www.smar.com.br
Veja a seguir um exemplo típico onde se tem os passos necessários à integração de um equipamento TT303 em um sistema PA e que pode ser estendido a qualquer equipamento:
- Copiar o arquivo gsd do TT303 para o diretório de pesquisa do configurador PROFIBUS, normalmente chamado de GSD.
- Copiar o arquivo bitmap do TT303 para o diretório de pesquisa do configurador PROFIBUS, normalmente chamado de BMP.
- Uma vez escolhido o mestre, deve-se escolher a taxa de comunicação, lembrando-se que quando se tem os couplers, podemos ter as seguintes taxas: 45.45 kbits/s (Siemens), 93.75 kbits/s (P+F) e 12Mbits/s (P+F, SK2).Quando se tem o link device, pode-se ter até 12Mbits/s.
- Acrescentar o TT303, especificando seu endereço no barramento.
- Escolher a configuração cíclica via parametrização com o arquivo gsd, onde é dependente da aplicação, conforme visto anteriormente.Para cada bloco AI, o TT303 estará fornecendo ao mestre o valor da variável de processo em 5 bytes, sendo os quatro primeiro em formato ponto flutuante e o quinto byte o status que trás informação de qualidade desta medição.
- Pode-se ainda ativar a condição de watchdog, onde após a detecção de uma perda de comunicação pelo equipamento escravo com o mestre, o equipamento poderá ir para uma condição de falha segura.
Conclusão
Vimos através deste artigo a importância da medição de temperatura na automação e controle de processos, um pouco da história da medição de temperatura e dos avanços tecnológicos dos transmissores de temperatura, assim como detalhes do TT303, Transmissor de Temperatura Profibus-PA.
Rreferências
- Manuais de Operação dos Transmissores de Temperatura Smar: TT301, TT302, TT411 e TT421.
- Web: www.smar.com.br e www.smarresearch.com.
- Controle & Instrumentação Edição 82 – “O protocolo digital HART”, César Cassiolato.
- Controle & Instrumentação Edição 93 – “Transmissores de Temperatura”, César Cassiolato.
- Pesquisas na Internet em diferentes sites sobre o tema Medição de Temperatura ( Todas as ilustrações, marcas e produtos usados aqui pertencem aos seus respectivos proprietários, assim como qualquer outra forma de propriedade intelectual).
|